Centrifugal Casting Bowl for Decanter Centrifuge
Product Specification
- Material: 2205 (022Cr22Ni5Mo3N), NAS 329J3L, UNS S32205, S31803 DIN/EN 1.4462, ASTM A240, ASME SA-240.2304, S32003, 2507, S32707, UNS S32304, EN1.4362, S32750 , EN1.4410.
- Size: Max. Diameter: 1600mm, Max. Length: 4200mm.
- Process: Smelting, Refining, Centrifugal casting, Heat treatment, machining, testing.
- Heat treatment: Annealing, normalizing, quenching or tempering
- Finish:Cast, rough machined, finish machined.
Product Name | Centrifugal Casting Bowl for Decanter Centrifuge |
Casting Method | Centrifugal casting |
Material Options | Duplex stainless steel, EN1.4362, EN 1.4462, EN1.4410 |
Material Standard | GB, ASTM, AISI, EN, DIN, BS, JIS, NF, AS, AAR, |
Casting Weight | 100-1500 kg |
Casting Size | Max Diameter: 1600 mm, Max Length: 4200 mm |
Casting Dimension Tolerance | CT9 - CT12 |
Casting Surface Roughness | Ra 50∽Ra12.5 um |
Machining Surface Roughness | Ra0.8 ~ 6.3um |
Service Available | OEM & ODM |
Certification | CE, ISO9001:2015, ISO19600:2014, ISO14001:2015, ISO45001:2018, |
Application | Decanter centrifuge, pusher centrifuge, disc separator, separation machine etc. |
Production Process
Centrifugal casting parts manufacturing involves a series of production processes in order to get finish products from raw materials. Weizhen Hi-tech has full in-house production facilities for the whole process, which strengthens Weizhen’ s abilities to meet any customer processing needs with consistent stringent quality control and quick turnaround time.
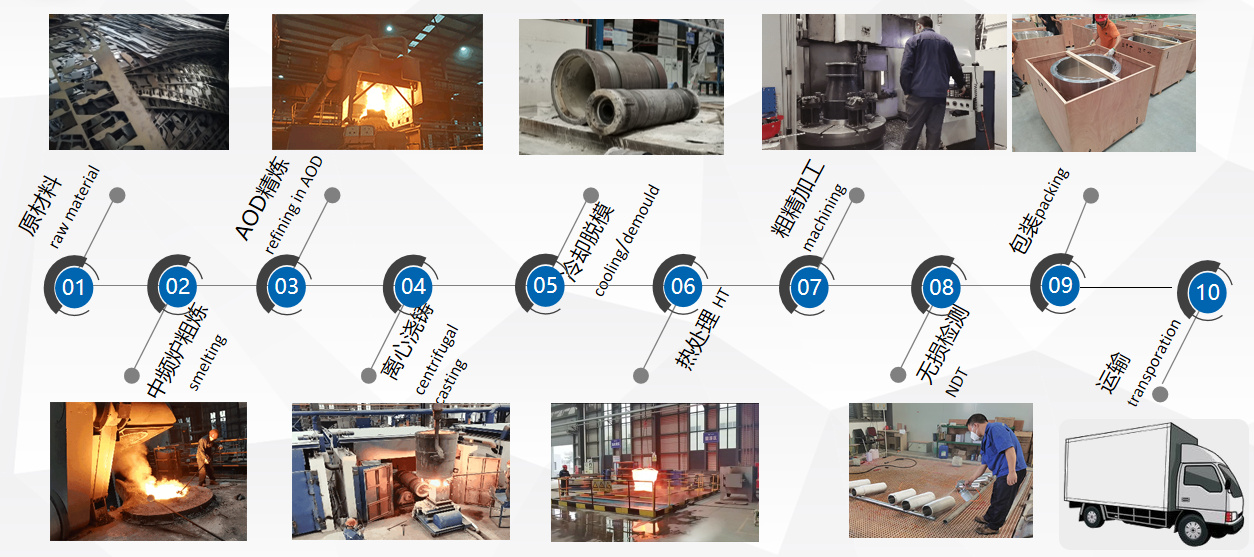
Smelting and AOD Refining
Weizhen Hi-tech has full in-house facilities for centrifugal casting manufacturing. Weizhen is uniquely equipped with AOD furnace for the refining of molten metal. A super low carbon, phosphorus, and sulfur content Steel alloy could be made upon request.
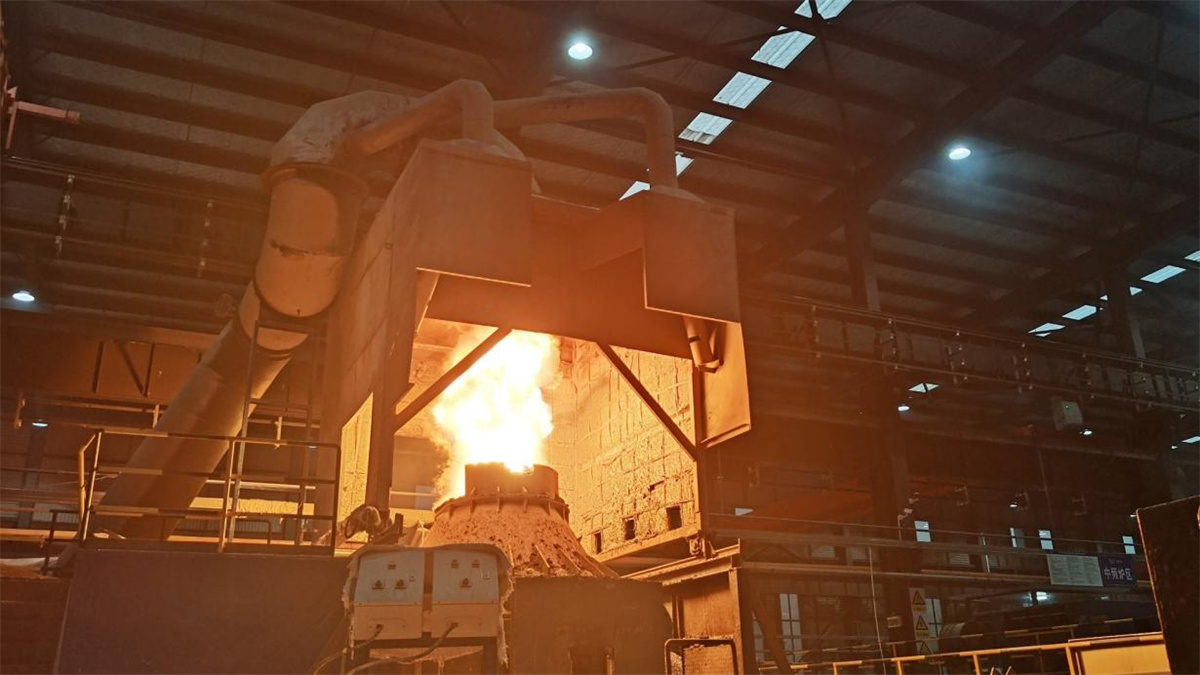
Centrifugal Casting
Centrifugal casting is a method used to produce metal products that are tubular, cylindrical, or annular in shape that require high quality, purity, and structural uniformity. Molten metal is poured into a spinning mold which forces the molten metal to the mold wall. The process is precisely monitored and controlled to assure the correct volume of metal is poured at the calculated flow rate and temperature. As the metal is poured, it conforms to the inside diameter of the mold and solidifies as it cools. Once solidified, the casting can be heat-treated, cut, and machined to customer specifications.
Weizhen has the largest horizontal centrifugal casting machine and vertical centrifugal casting machine in China. The maximum casting diameter could be as long as 1600mm. The single biggest collection of more than 300 centrifugal casting molds enables Weizhen to meet any size requirements.
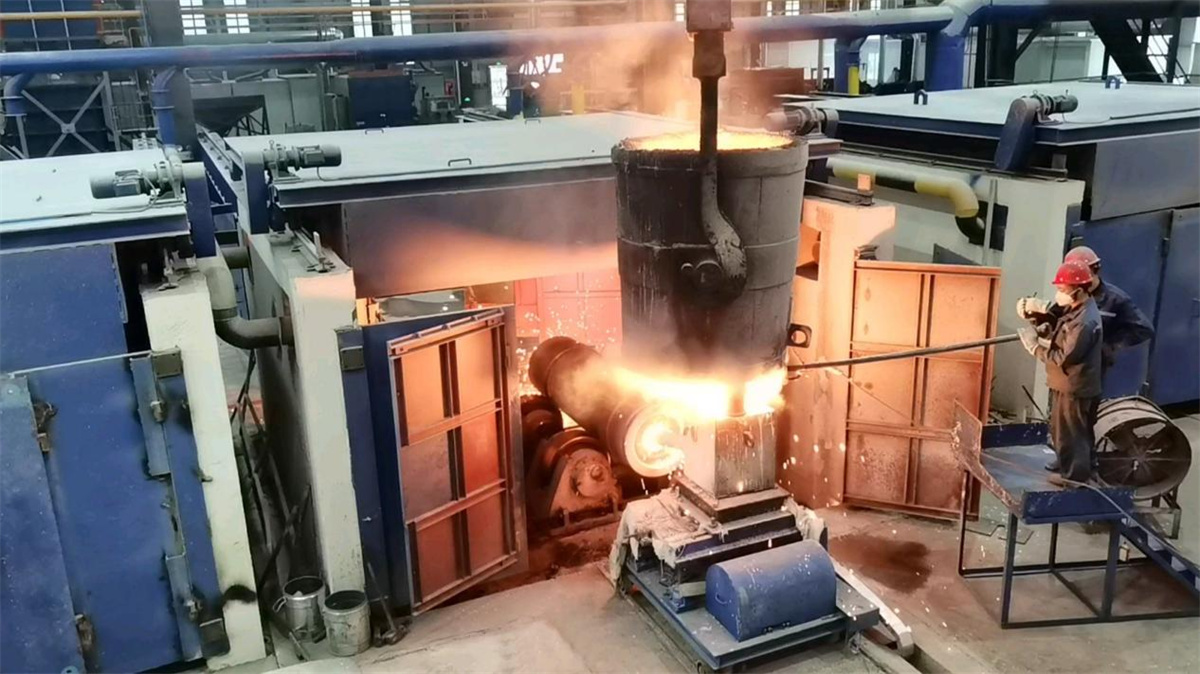
Heat Treatment
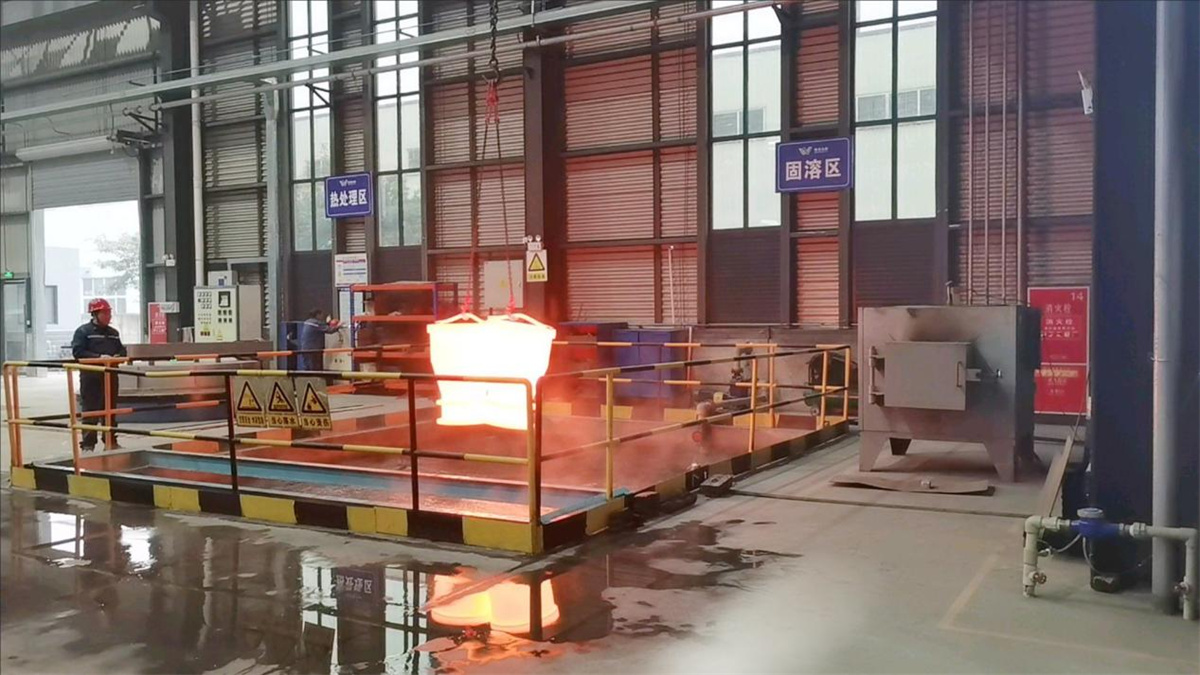
Machining
Weizhen is equipped with over 20 machines for the processing of stainless steel casting parts and components. State-of-the-art cutting machine, shot blasting machine, horizontal lathe, CNC horizontal lathe, CNC vertical lathe, CNC Gantry milling machine, Radial drilling machine, Digital display boring and milling machine are all installed in the factory.
The fully set up facilities enables Weizhen to provide customers with a highly convenient and efficient one stop service. The parts can be delivered as cast, rough machined or finish machined.
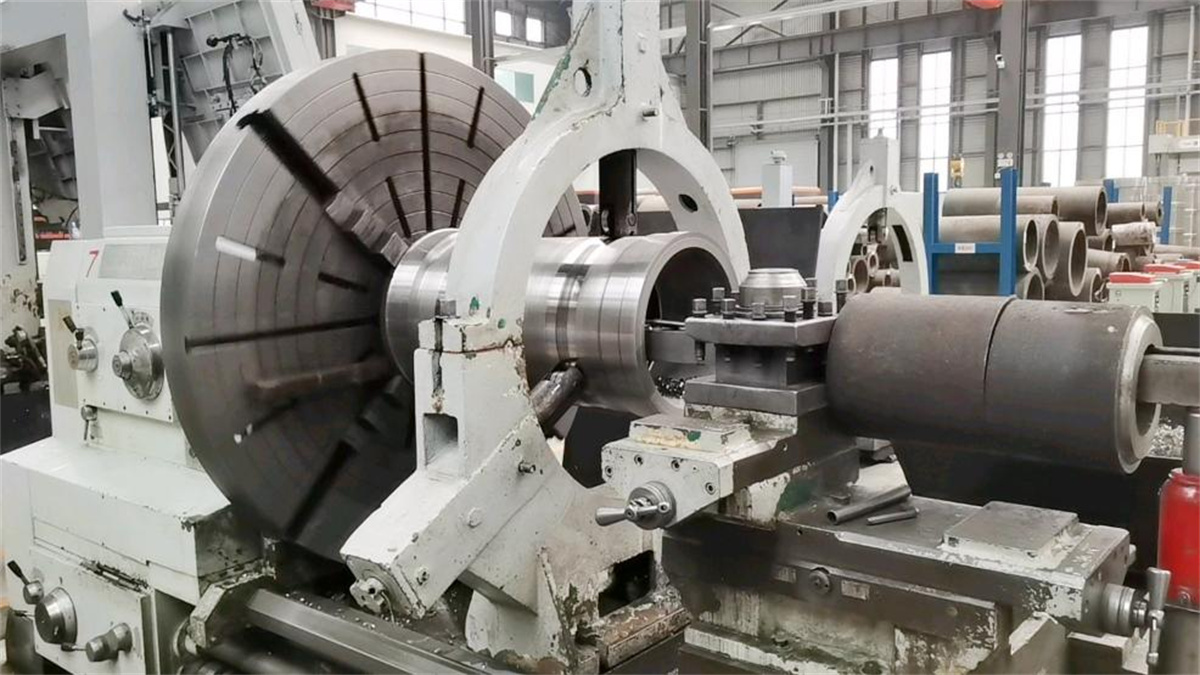
Testing
Product quality test is essential in the centrifugal casting industry for customer satisfaction. Weizhen conducts strict checking and testing through out the whole production process. Weizhen runs a series of chemical and physical testing, NDT testing, dimensional inspection to ensure each product meet customer requirements or standards.
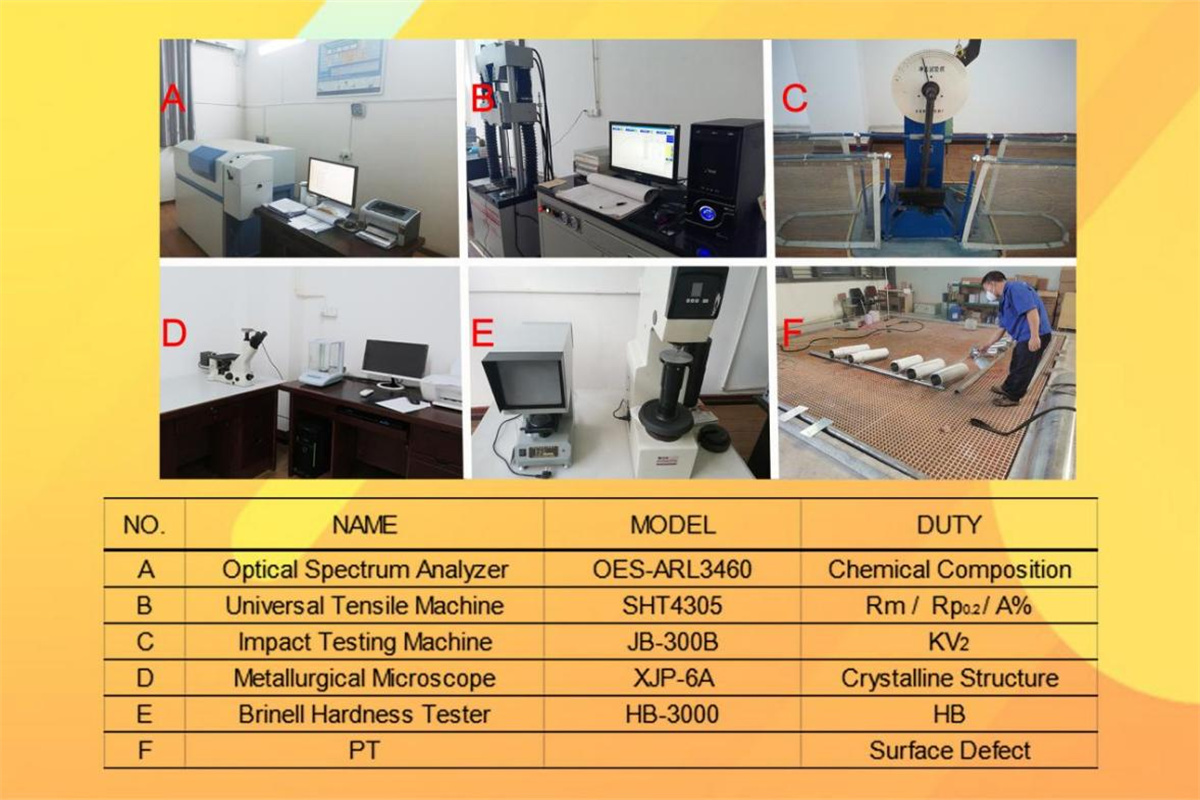
Certification & Quality Management
The team of Weizhen engineers understand stable and excellent product performance is key to the success of our customers. Weizhen utilizes the latest technology and quality management system to ensure our products are reliable and meet the highest standards. With committed responsibilities to customer, the society and employees, Weizhen is certified and strictly operates with multiple management systems to ensure a sustainable future.
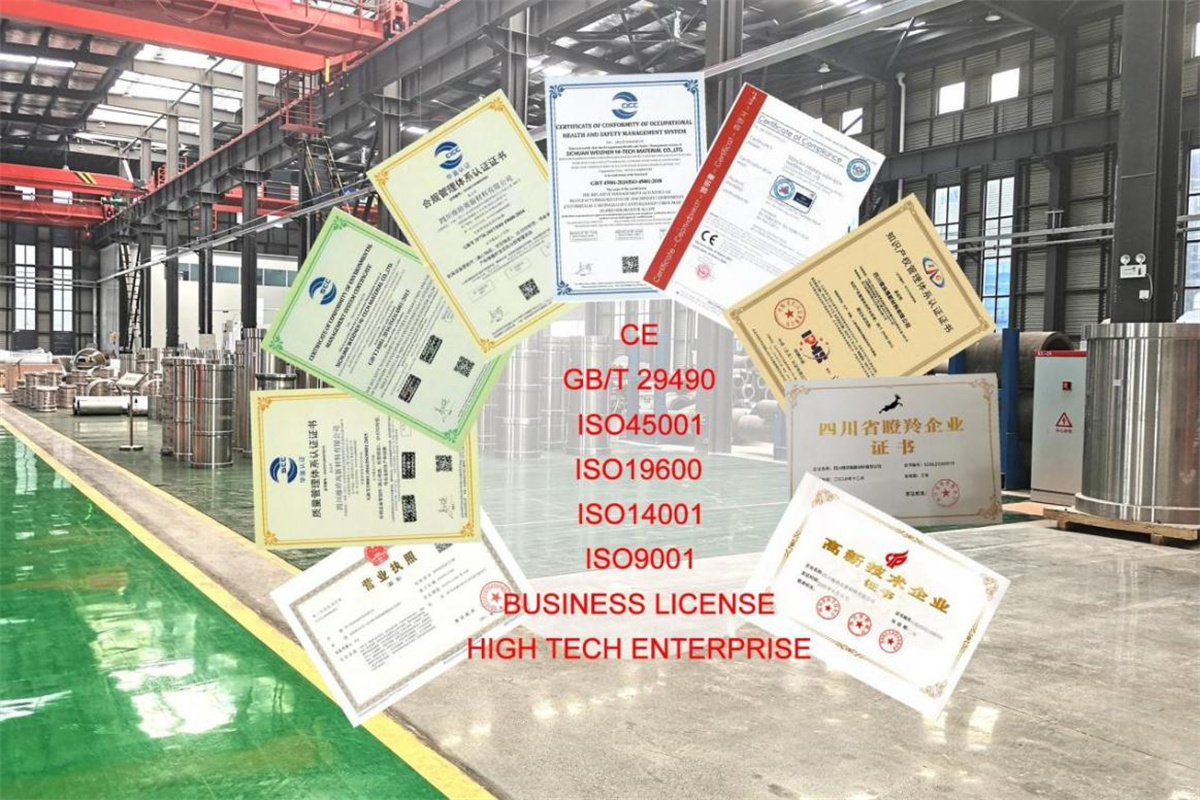