Bowl Set for Decanter Centrifuge
Product Specification
- Material: Duplex steels (standard duplex, lean duplex, super duplex), austenitic, nickel-based alloys.
- Size: Max. Diameter: 1600mm, Max. Length: 4200mm.
- Process: Casting simulation, Smelting, Refining, Pouring & centrifugal casting, Heat treatment, machining, testing, packing.
- Heat treatment: Annealing, normalizing, quenching or tempering
- Finish:Cast, rough machined, finish machined.
Product Name | Bowl Set for Decanter Centrifuge |
Casting Method | Centrifugal casting |
Material Options | 304, 304L, 316, 316L, SAF2304, SAF 2205, SAF2207 |
Material Standard | GB, ASTM, AISI, EN, DIN, BS, JIS, NF, AS, AAR, |
Casting Weight | 100-1500 kg |
Casting Size | Max Diameter: 1600 mm, Max Length: 4200 mm |
Casting Dimension Tolerance | CT9 - CT12 |
Casting Surface Roughness | Ra 50∽Ra12.5 um |
Machining Surface Roughness | Ra0.8 ~ 6.3um |
Service Available | OEM & ODM |
Certification | CE, ISO9001:2015, ISO19600:2014, ISO14001:2015, ISO45001:2018, |
Application | Decanter centrifuge, pusher centrifuge, disc separator, separation machine etc. |
Production Process
Weizhen Hi-tech has full in-house production facilities for the whole production process for centrifugal casting manufacturing, from process designing, casting simulation, steel smelting, to steel AOD refining and pouring, heat treatment, machining, testing and inspection.
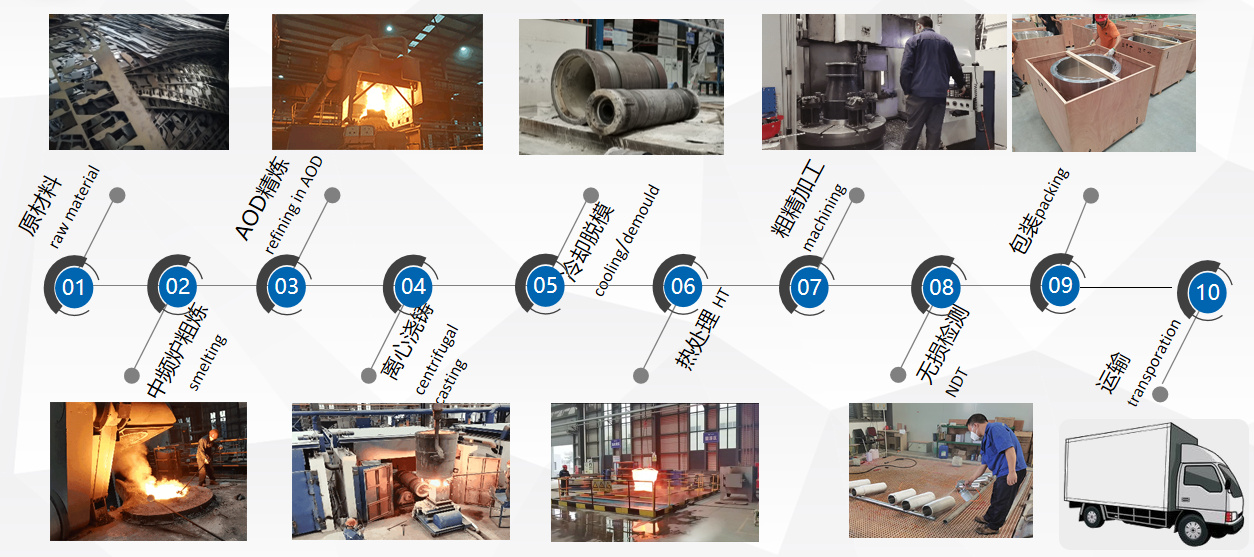
Smelting and AOD Refining
Weizhen is uniquely equipped with AOD furnace for the refining of molten metal besides normal medium-frequency induction furnaces. The molten metal after refining is much more pure with super low carbon, phosphorus, and sulfur content, providing better mechanical and chemical performances for the casting parts.
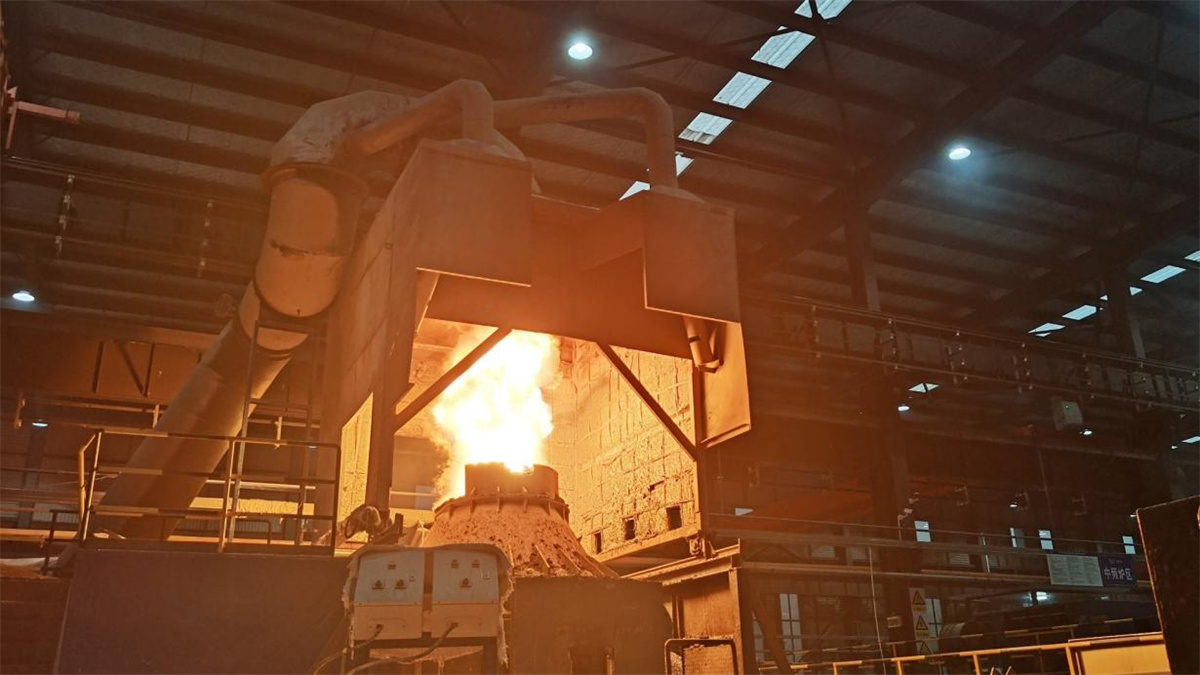
Pouring & Casting
The molten metal is poured into a cylindrical mold that rotates at a high speed. The centrifugal force generated by the rotation forces the molten metal to spread evenly along the inner surface of the mold, creating a hollow, cylindrical shape as it solidifies. Centrifugal force causes impurities and lighter oxides to migrate to the inside diameter of the casting which, upon solidification, are easily removed by CNC machining and processing.
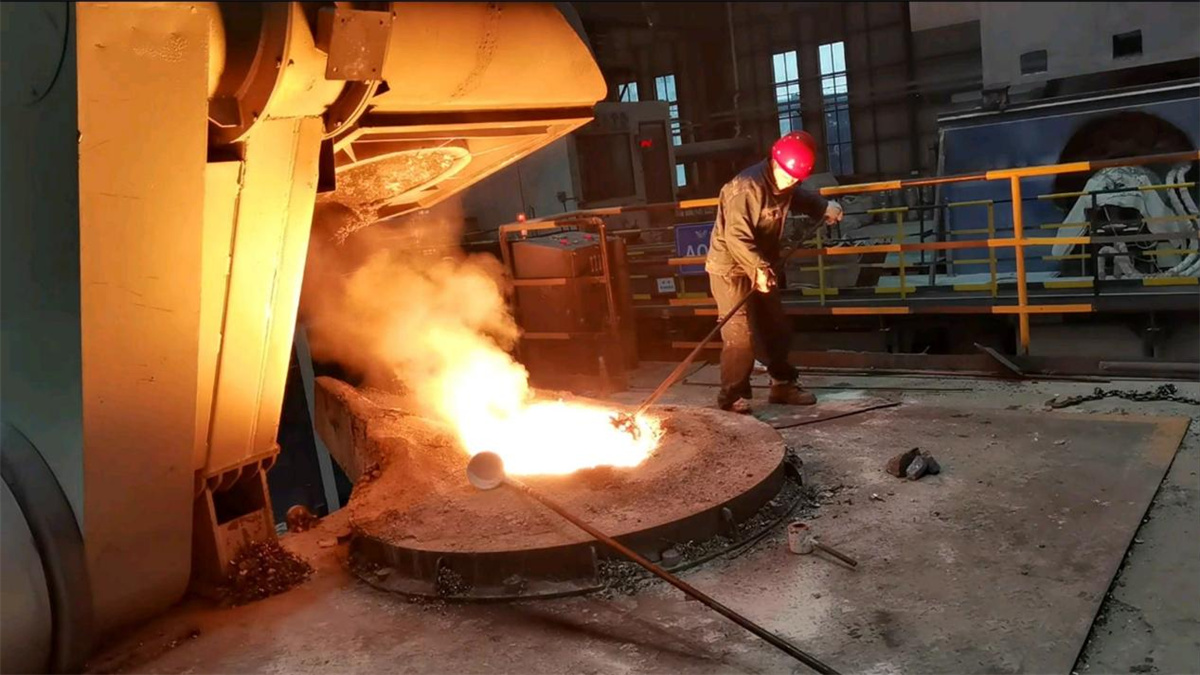
Heat Treatment
Heat treatment is critical to the properties and quality of the steel castings. Weizhen is equipped with advanced 1200 °C heat furnaces and car type furnaces for the heat treatment. The casting parts are precisely heat treated to achieve the desired properties inside the factory.
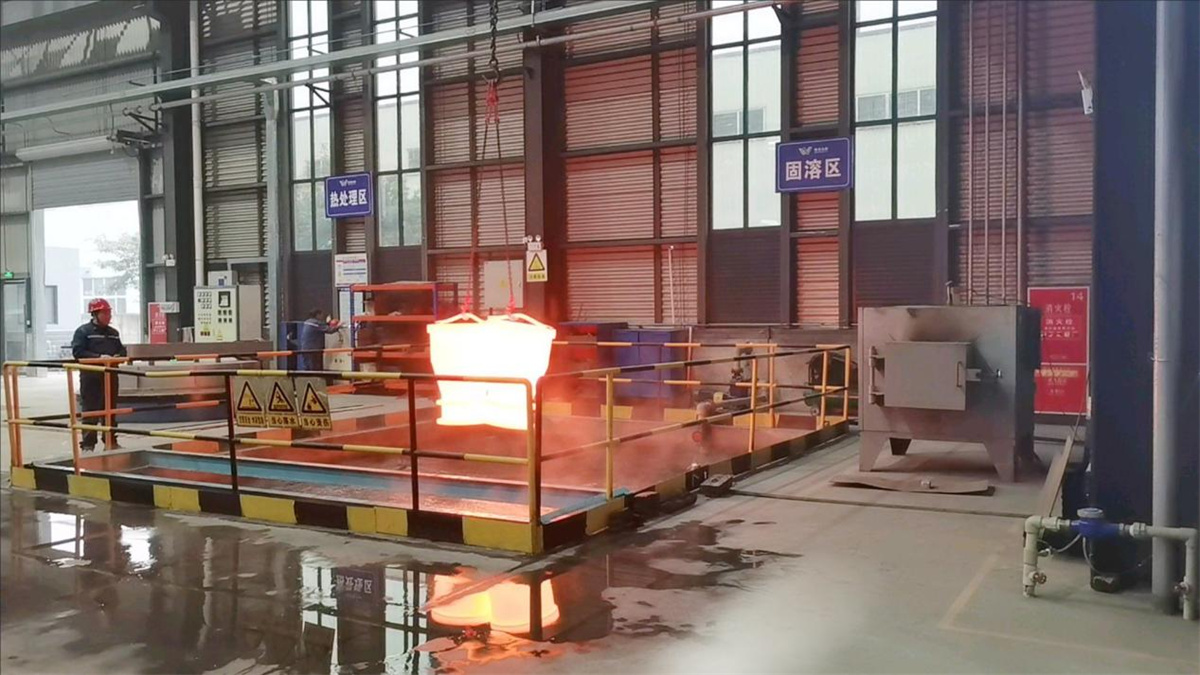
Machining
The centrifugal casting blanks need to be further machined & processed to meet customer requirements. Weizhen is equipped with all sorts of machining equipment for the processing of stainless steel casting parts and components. State-of-the-art cutting machine, shot blasting machine, horizontal lathe, CNC horizontal lathe, CNC vertical lathe, CNC Gantry milling machine, Radial drilling machine, Digital display boring and milling machine are all installed in the factory. The products could be delivered as cast, rough machined or finish machined.
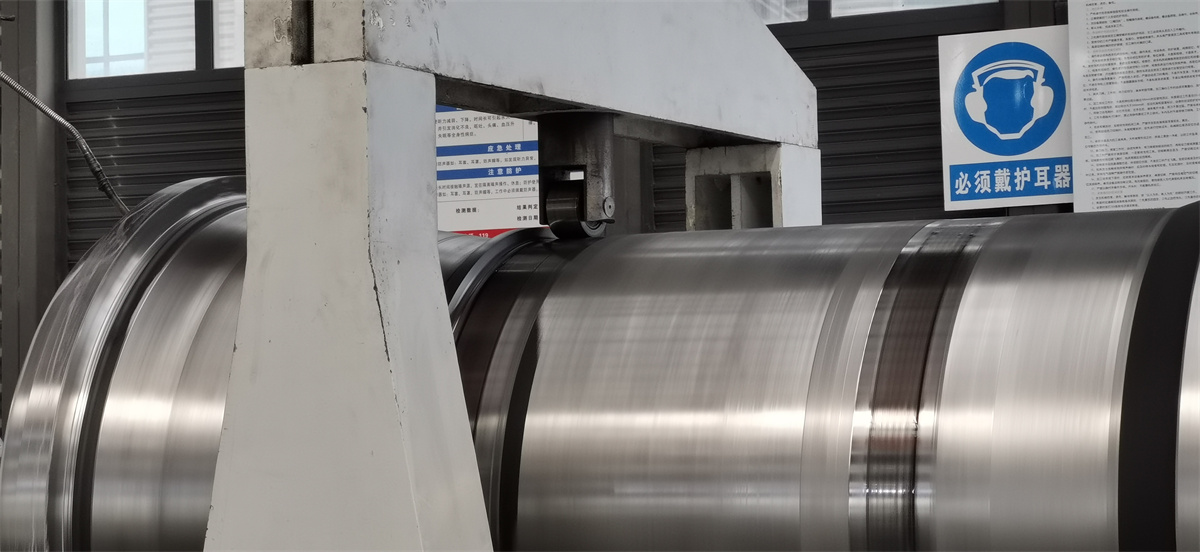
Inspection & Testing
Casting parts need to be tested and inspected before delivering to customer. Weizhen conducts strict checking and testing through out the whole production process to ensure best product quality and customer satisfaction. The tests and inspections Weizhen provides include, but not limited to, chemical analysis, physical properties, dimensions, PT, RT, three coordinates, 3D Scan.
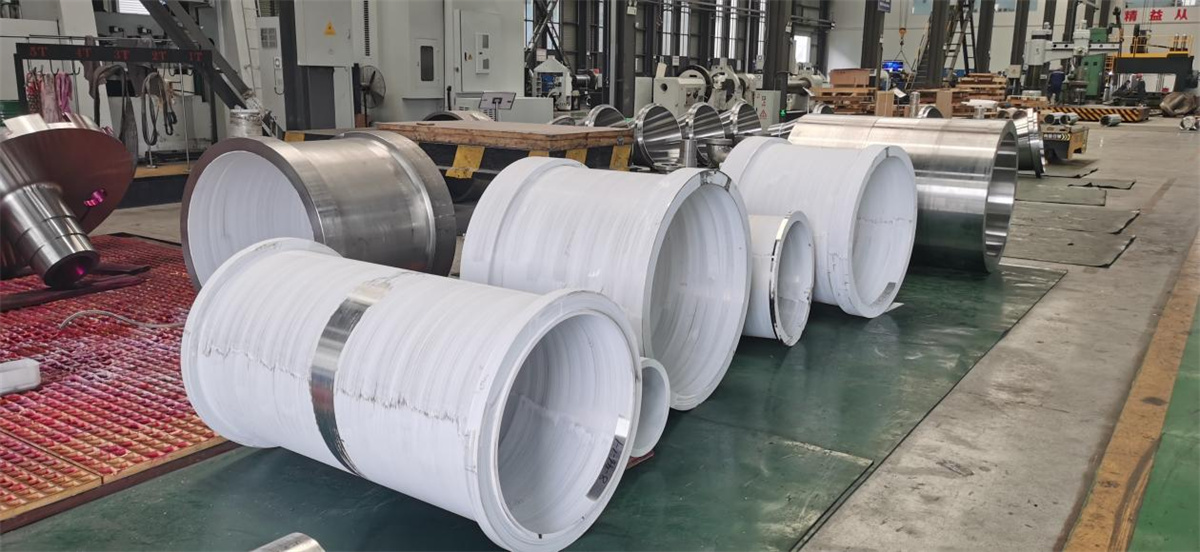
Certification
With committed responsibilities to customer, employees, the society, and the environment, Weizhen is certified and strictly operates with multiple management systems to ensure a sustainable future. The main certification includes ISO9001 quality management system, EU product CE certification, ISO14001 environmental management system certification, OHSAS18001 occupational health and safety management system certification, GB/T29490 intellectual property management system certification, and ISO19600 compliance management system certification.
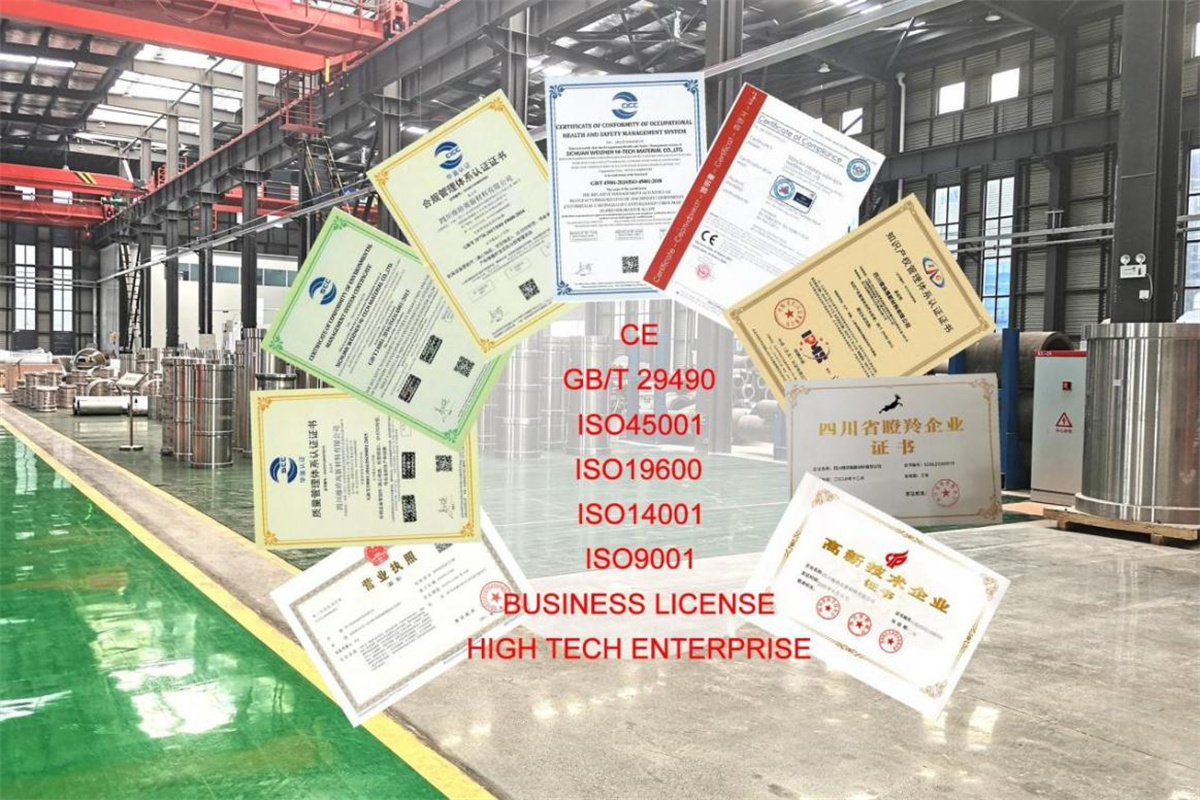